THE HISTORY OF PAPERMAKING
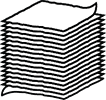
Our intellectual and material literacy are dependent on paper. This type of writing material rescued our hereditary knowledge from the destructive hand of time. With paper’s help we can further augment this heritage and bequeath many things to posterity. Therefore it is appropriate that paper, which has patiently served mankind’s progress, should speak about itself and its past.
Prior to the invention of paper, various materials were used for writing. First soft clay, which transformed into terracotta tablets, was used. Later it was followed by large plant leaves, animal skins, parchment, waxsheets and especially papyrus. The latter eventually gave paper its name. The Egyptans found a native reed-like plant, the so called papyrus, and they used its phloem for making rolls suitable for writing. Some foreign museums exhibit 5500 year old papyri
This type of writing material rescued our hereditary knowledge from the destructive hand of time.
^ Rag selection, material preparation
When papyrus almost disappeared from Egypt, there grew a need to find an other raw material. Parchment was the material that quickly replaced papyrus rolls. As a matter of fact, parchment was the depilated, flattened skin of various animals. Lamb, goat or calf skin were refined to create a very soft and fine surface to write on. The first known skin processing plant was established in Pergamon in Asia Minor. Parchment’s great advantage was that during folding it does not get broken. This way it was possible to knit more sheets into one book.
The paper we use today has Chinese roots and was invented by Cai Lun, a courtier to the emperor Hedi in AD 105. He was the one who recommended to the emperor that the heavy bamboo tablets and costly silk with paper be replaced. The emperor accepted the idea and decreed the dissemination of papermaking.
^ Mold and watermark making
The paper was made of plant fibers, a plate suitable for writing, simply a fibersheet. Chinese papermakers used mulberry tree phloem, bamboo fiber, Chinese grass, and other plants as raw material. A small amount of rag scrapings were mixed in. The fibers were cooked to loosen them up then they were pulped in a mortar. The pulp then was diluted with water and the fibers were planked with a bamboo sieve (so called “mould”). A thin layer of pulp was scooped up on the mould’s surface, throwing off any excess (called “throwing the wave”) and then, while holding the mould perfectly level, shaking it from side to side and front and back as the water drained through (this “shake” when done correctly, interlocks the fibers into a smooth, even mat that is said to have good formation). The freshly formed sheets were then transferred on wood boards: one layer of paper sheet, one layer of wood board, another layer of paper, wood board again and so on. This stack was then placed in a hydraulic press under tons of pressure and the bulk of the water was squeezed out. The paper was then ready to be dried either in open air or on heated walls. To make the sheets’ surface writable, a thin layer of rice starch was brushed on them.The main phases of the technology are as follows: pulp creation, sheet formation, drying, surface treatment. These phases have not changed since their invention. Cai Lun’s methods were improved over the centuries but during the last 600 years it has barely changed.
^ Papersheet forming, pressing
In the following centuries more paper manufacturing facilities were built in Syria, Pelestine, Persia, and in the towns of India ruled by Arabs. In the 10th century A.D., in the footsteps of conqueror Arabs, papermakers appeared in Cairo. Around 1100 the first signs of papermaking were discovered in the Moroccan town of Fez. Flax, hemp, cotton, and rag scrapings were used as raw materials. After sorting, these raw materials were putrefied and boiled in water then pulped in a stone mortar. The dipping bath was made of wood so the pulp, which was diluted with water, could be poured into it. The papermakers formed the papersheets with dipping sieves made of reed which afterward were layed on wooden boards and pressed. The drying occured outdoors by laying the wet paper sheets on walls. As an after-treatment, the paper was glued by dipping it into a wheat starch bath. The dry paper wasthen flattened out with a glass sheet or agate. Color paper was produced by the means of surface painting using vermilion for red, carbon paper for blue and saffron for yellow.
The Arab-Moorish culture also disseminated the knowledge of paper in Europe. Paper was already a commodity in Spain around 860 and in Italy in 1100. The Moors in Spain, in order to avoid transporting ready-made paper, established paper manufacturing mills. The first one was established around 1100 in Xativa next to Valencia. Papermaking started its journey in Christian Spain only in 1260. Italy imported paper from Egypt through Sicily and in 1109 it was already used in Levante. Its widespread distribution was helped by the fact that papyrus manufacturing ceased to exist around 950 because the plant became extinct in Egypt. In Sicily it was not planted in commercial quantities. The first Italian paper manufacturing mill started its operation in Fabriano.
“We make imperishable things, books from rags that always lives with us.”
^ Glueing, after-pressing
The evolution of papermaking in Europe is somewhat different from that in the Arab world. Europe’s progression is characterized by the following: the pulping machine was invented, the straining dipping sieveis formed for paper sheet creation and the wire water mark is invented. Pressing and water squeezing are done between felt sheets with a bolt press, drying occurs in the air on wooden rods, ropes, and drying lofts and surface treatment is carried out by dipping the paper into gelatin or other glue.
The need for paper in the XV – XVI centuries dramatically increased due to the general dissemination of writing and the invention and widespread use of printing (Gutenberg). Papermaking tecniques also further developed.
For the energy hungry pulping and mashing work of a papermill some sort of water energy is needed. The papermill usually is a one or two story building with a drying loft with approximately 3000-7000 cubic air meters. The water is driven to water wheels measuring 3-4 meters in diameter and .7 meters wide via a flood gate or water canal system. The wheels are equipped with bevel-gear, pegs, and levers to run the machinery. The papermill is the home of a ragstorage, glue kitchen, drying loft, paper storage, dipping and felt workshop, locker rooms and bathrooms, and even living quarters.
During raw material preparation rag selection, cleaning, and cutting were followed by white lime treatment or putrefying. Additives were created by gaining white lime from slack lime and by boiling glue with alum. to produce 1 kg of paper, 2.3 kg of rag, 20 % lime (4 % potash for leaching), 21 % glue for the boiling, and 0.4 % alum were used. For further processing the mash was dumped into the pulper and the limed material was pulped for 36 hours, the putrefyed material for 12 hours or for 3-4 hours in a Hollander beater. After this the semi-ready material was stored for 2-4 weeks for further desintegration. The ready-to-use material also was dumped in the pulper where it was being pulped for 12-14 hours or for 5-7 hours in a Hollander beater. In the last hour it was mixed with white lime, and in case of colored paper with coloring matter. It was then stored in a desintegrating container. In the dipping bath, the papermaker placed the sieve (mold) into the pulp, then with a slow but steady movement lifted the sieve above the water level, creating a thin pulp layer on the top of the mold. After a short gentle wiggling of the mold – so the mold stopped dripping – the papermaker placed the pulp layer together with the pulp layer on a felt sheet.
^ Drying
Then he pressed the mold against the felt and with a sudden motion he picked up the mold from the felt. What was left behind is the wet paper sheet on the felt. The so called “duzma” (181 paper sheets between 182 felt sheets) then was placed in a press where it was pressed for 3-4 minutes. Then the paper sheets were removed fom the felt sheets and were placed in the “white duzma”, 5 or 6 of which were put in the press again for another 8 to 10 hour pressing. The papers were then hanged on a rope or a wooden rack to dry in 2-4 sheet groups. The paper then was dipped in gluey water and was dried. The next step was to rub the paper surface with a smoothing stone or by the means of paddling, 4 or 5 times per sheet. From the XVIII century both methods were replaced with multiple extrusion. It was followed by defect selection, folding, and baling. The watermark was known and used during the entire era and every single paper was marked. The object of a watermark was mostly to identify the papermill, the papermaker, the named or symbolic marking and the type of paper used.
^ Dry pressing, selection
There were a few people who were studying the history of manual paper making in Hungary. A special mention goes to István Bogdán who went a great distance in analyzing rear documents found in the National Archives and even beyond tried to locate all of those paper mills that operated in historic Hungary.
It’s also worth to note the work of Lajos Nándor Varga whose wood engraved watermarks form a very valuable part of the Hungarian cultural history. Paper mills could function effectively only in places with clear, running streams with sufficient slope and free of flooding. During the planning phase it was important that the available water was chemically soft.
In general the founding dates are uncertain and the help offered by watermarks can be used multiple times. The first Hungarian paper mill was founded in the first half of the 16th century in the town of Levoca (Lőcse in Hungarian) which burned down but later was restored again.
Our second known paper mill was mentioned around 1539 in Brasov (Brassó in Hungarian) linked to the name of János Honter. There were mentions of functioning paper mills in Bardejov (Bártfa in Hungarian) in 1548 and in the heart of Transylvania in the city of Cluj Napoca (Kolozsvár in Hungarian) starting in the year of 1550. There was a paper maker under the name of Jörg in the city of Sibiu (Szeben in Hungarian) dated back to 1555. The location of the next paper mill was Liptovsky Michal (Liptószentmihály in Hungarian) starting from 1596.
In the beginning of the 17th century in the towns and cities of following counties of Upper Hungary (today’s Slovakia) started to turn the wheels of paper mills: Szepes, Sáros, Pozsony, Bars, Túróc, Abauj, Gömör. Later Transylvanian counties joined in as well: Alsó Fehér, Beszterce, Száz Sebes Szék, and Torda.
In the 17th century overall 33 paper mills were reported about mostly in the North. In the 18th century our paper industry had difficulties to progress due to the very unfavorable political end economic environment. The pace of progress started accelerating only from the 30’s when paper mills were founded in Baranya, Sopron, Vas, and Veszprém counties. From other regions of the country only 4 counties had the bragging rights of claiming to have paper mills: Bihar, Pest, Temes and Zágráb.
In 1802 after the 3rd attempt finally a new paper mill was created in Diósgyőr (which is is still functioning even in these days as a modern day paper mill and factory). To sum it up these last 300 years had delivered nice results: we have the knowledge of a total of 158 paper mills that were founded and started operating in this era. We can state that our nation’s paper making and producing capability and capacity almost fully satisfied the domestic needs.
“The creation of script carrier materials of art retains any other types of art.”
Contact
Address:
Vinczemill Kft.
2000 Szentendre,
Anna street 16.
Vinczemill Kft. – © All rights reserved
Design: Pletser Cecília
Sitebuild: WahrDesign